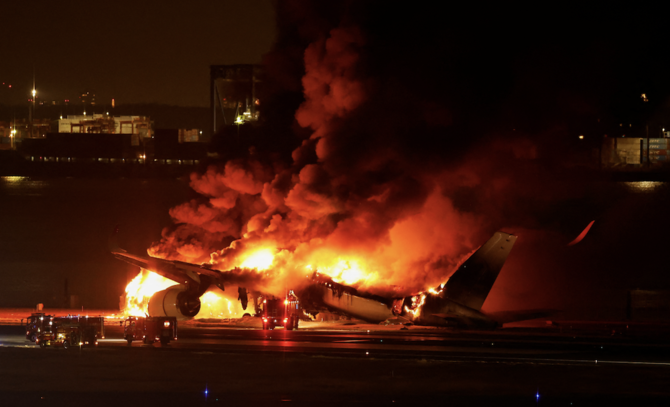
The use in commercial aircraft construction of fiber-reinforced polymers, or composite materials, is under the microscope after last week’s near disaster on the runway at Haneda Airport in Tokyo.
A Japan Airlines Airbus A350 collided with a smaller Japanese Bombardier Dash-8 coast guard plane as the passenger jet was landing while the smaller aircraft was attempting to take off.
Fireballs erupted from both aircraft as JAL flight 516 continued down the runway covered in flames and emitting gray smoke, an indicator of low toxicity. Within 20 minutes, all 379 passengers and crew slid down emergency chutes and survived. The pilot of the coast guard plane escaped with injuries, but his five crew were killed. Airbus investigators from France are examining the plane’s wreckage.
The fire is being viewed as a key test case for airplane fuselages or hulls made from carbon-composite fibers, as found on the A350 and the Boeing 787 instead of conventional aluminum “skins.”
This incident was the first in which severe damage was caused to an Airbus A350, among the industry’s newest large passenger planes. In this case we saw the composite materials burn, which actually helped to save lives. So the airline industry is taking a very close look at this crash and possible adjustments that need to be made to current fleet procurement by commercial aviation companies.
Significantly, composites have been on aircraft for decades in wing-to-body fairing panel assemblies, rudders, and tail sections. Interior components contain composites. Now the entire aircraft, especially the fuselage, may contain these materials. Today’s modern commercial aviation passenger jets are still made from metal, but aviation engineers have been increasing the proportion of carbon-fiber composite materials to reduce weight and increase efficiency.
Modern aircraft made of carbon-fiber composites burn in a unique way. The twin-engine, twin-aisle A350 is used by a number of long-haul international carriers. More than 570 of the aircraft are in operation around the world. When this type of plane burns, the polymer materials create an insulating layer protecting the escaping passengers from the heat of the fire. If this incident had involved an older aircraft, the effect of the fuselage’s roof acting as a “heat shield” would not exist, leading to potential casualties.
The Japan incident was a prime example of construction material, fire safety and evacuation procedures that combine to make today’s aviation industry fly better and smarter.
Dr. Theodore Karasik
Passenger compliance with instructions when an aircraft catches fire is also key to saving lives. The 20 minutes of escape time to evacuate the plane is part of the analysis of how the plane’s ecosphere protects passengers during accidents. Importantly, passengers from different societies will act in different ways during a safety hazard escape.
Japanese society is well structured and crowd control measures are well ingrained in public spaces. Passenger videos (key for evidence of internal burning and smoke patterns) of last week’s incident showed people covering their mouths with handkerchiefs as they ducked down and moved toward the exits and down their emergency slides without bags, purses or other hand-held items. Each passenger took family and personal responsibility. Thus, a composite commercial aircraft gives the escaping passengers a better chance at survival when they comply 100 percent with airline emergency regulations. Here, the composite nature of the aircraft guaranteed additional security for the passenger.
The aviation industry watches these developments closely. There are three main points about aluminum or composite hulls and burning and integrity of the aircraft when there is an accident or crash. First, fuselage skin is an excellent fire barrier and resists flame penetration far longer than an aluminum fuselage. Second, the toxic gas levels produced in a post-crash fire scenario are similar for both a composite fuselage and an aluminum fuselage. Finally, there needs to be a guarantee that no prolonged burning or re-ignition of the composite skin will occur. These are all regulatory and compliance issues that the airline industry itself designed with the help of aviation experts and physicists.
When a composite plane burns, it requires a specific amount of water to put out the flames. Interestingly, more water is required at airport fire and rescue services in preparation for a composite hull fire. Previous incidents with composite hull fires bring the water issue into focus. A fire on an American B-2 bomber over a decade ago helped scientists determine temperature and burn rate issues, and how much water would be needed for a potentially hotter fire. This investigation led to many airports having to increase their water reserves and add new training in fighting composite fires. There are hundreds of scenarios for crashes and accidents, so the engulfing of a composite hull brings new clarity to airport safety requirements.
Overall, composite materials save lives and help with efficiency of safety in more commercial aviation. The Japan incident was a prime example of construction material, fire safety and evacuation procedures that combine to make today’s aviation industry fly better and smarter.